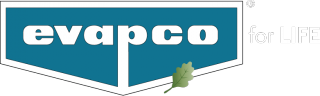
EVAPCO’s MT series of closed circuit coolers is the first in the industry to feature composite fibreglass panels formed entirely by an advanced, environmentally friendly, LRTM closed mould manufacturing process. The advantages of this process include high quality solid laminate construction, uniform part thickness, low part variation, complex shapes, and reduced styrene emissions.